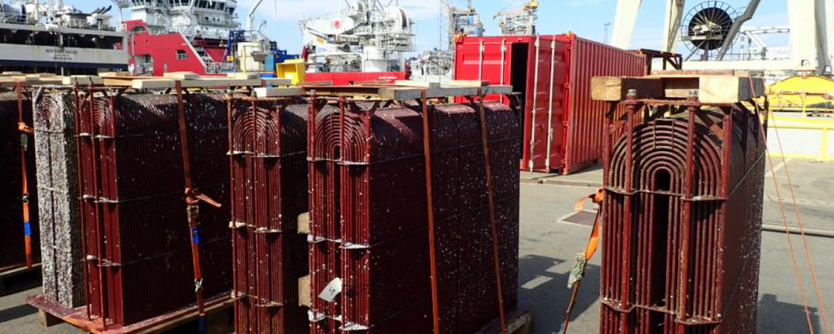
Box cooler corrosion
Box coolers became popular on certain types of vessels from around 2005. Norwegian Hull Club has experienced corrosion damage cases involving box coolers since 2014, mainly occurring between one-and-a-half and three-and-a-half years after the first special survey (five-years).
In our experience, the damage scenario is complex. As such, we believe it is crucial that stakeholders interact with each other in order to prevent or limit damage. Stakeholders must understand the importance that their systems and components have in relation to other parties’ equipment / components in a box cooler system compartment.
KEY FACTORS
A ship builder’s choice of hull and the quality of its material are key factors. The hull is protected from corrosion by primer and anti-corrosive paint delivered by a paint manufacturer and applied by a shipyard (preferably with qualified supervision from the paint supplier). Anti-fouling paint is added to limit marine growth. The material used to make box cooler tubes varies by manufacturer, with aluminum brass being a popular choice. This is coated with a suitable paint to isolate the metal on the tubes from seawater, preventing corrosive electrolytic currents that will affect an unprotected hull. An Impressed Current Anti-Fouling (ICAF) system is installed to prevent or limit marine growth on the tubes by introducing copper ions to the sea water, dissolved from copper rods. Sacrificial zinc or aluminum anodes are installed to protect the hull when the paint system becomes worn and/or fails.
IMPACT
The design, manufacture, installation, quality and quantity of these systems and components - and their effect on each other - has an impact on the box cooler compartment. In cases The Club has dealt with, there are often indications of a lack of “interface and/or understanding” between the various stakeholders.
The box cooler compartment is also affected by the vessel’s operational pattern and location, docking intervals and maintenance by the shipyard / service companies when in dry dock. These factors must be taken into consideration when planning and executing maintenance of the box cooler compartment. The quality of hull, box cooler and ICAF system cleaning and maintenance depends heavily on the qualifications and knowledge of the contractors / service companies involved.
Since 2014, The Club has been involved in several claims on box coolers and been presented with various cause considerations for similar damages. Having accumulated competence via survey reports, service reports and dialogue with owners, makers and repairers, The Club is of the opinion that corrosion to a vessel’s hull and / or box cooler flanges is most likely a delayed effect of box cooler tubes being improperly cleaned and/or painted, or incorrectly cleaned and not painted (see Note 1), during maintenance work in dry-dock, and often during the first special survey (after five years).
The improper and / or faulty cleaning / painting of the box cooler tubes in dry dock can result in them being only partially coated when the vessel resumes operations. While this does not affect the tubes themselves, they will - if there are defects in the paint on the vessel’s hull and the cathodic protection from the vessel’s anodes are spent or inefficient – act as cathodes, with the vessel’s hull becoming an anode. When this happens, the hull’s steel plates (or the steel flanges of the box coolers) will eventually become wasted.
MAINTENANCE
Such substandard maintenance may have been performed accidentally by an individual or by the shipyard due to a lack of knowledge and/or procedures. The vessel’s crew and / or the superintendent responsible for supervising the work in dry dock may have had limited knowledge regarding the task, so was unable to pick up on any errors. Additionally, the owners would be unable to establish sensible procedures and specifications for maintenance and repairs due to them being unaware of such shortfalls.
The rate and magnitude of corrosion is very difficult to predict or verify as it is affected by many factors, including:
• Extent of the damage to / loss of the coating on box cooler tubes
• Extent of the damage to coating of the hull / and or box cooler frames
• The amount / quality / location of sacrificial
anodes
• The functionality of the ICAF system (prevent fouling on the box cooler tubes)
• The “integrated” ICAF system has proven to be particularly vulnerable
• The fouling level of the box cooler depends on:
a) The equipment connected to the cooler, i.e. the temperature of the cooling water in the box cooler tubes; b) Paint type and quality of the box cooler tubes; c) Paint type and quality of the vessels hull and box cooler flanges; d) Trade / speed of vessel;
e) Seawater (salt content / temperature)
• Air pockets in the box cooler compartments (See Note 2)
• Possible unknown factors
As mentioned, the consequences of improper cleaning / the condition of the painting of the box cooler tubes appears to have been initially unknown to many stakeholders. Knowledge of all the possible contributing factors, their complexity, as well as the severity of the problem as a whole, has also gone unrecognized. However, since early 2016 when classification society DNVGL issued a technical and regulatory newsletter (02/16), knowledge and experience has steadily increased. In 2018, Norwegian Hull Club issued Casualty Information Newsletter No.99 on the issue. Both of these documents have been used in compiling this newsletter.
MAINTENANCE RECOMMENDATIONS
• Maintenance should be performed according to maker’s recommendations
• Cleaning in situ, although difficult, may be performed by a chemical process
• If not, the coolers must be removed to enable proper cleaning and inspection
• Coating must be done onshore as it requires specialist skills and equipment
• Owners must carefully consider the type of paint to be used, based on expected lifetime considerations. Consult with the paint supplier
• Box coolers cannot be cleaned the same way as the hull; a) it must be done diligently and one should avoid, or be very careful with, high-pressure washing of the tubes; b) Scraping of the tubes should be performed with soft tools only; c) Chemical cleaning on site may be the preferable option
• Box coolers cannot be painted the same way as the hull: a different type of paint is required, while access to enable proper painting of the tubes is very limited (a specialised process is required to re-coat the tubes)
• Some people may still be unaware of the consequences of improper cleaning / painting of box coolers. Ensure that the dry-docking specification clearly states what should be done and how, and that this is understood and executed correctly by the shipyard
• Ensure qualified supervision during maintenance work
ICAF system (Impressed Cathodic Anti-Fouling system)
The box cooler compartment (sea chest) with equipment consists of many different materials, of which a number can cause galvanic corrosion if not isolated from one another: copper anodes (ICAF rods), aluminum or zinc anodes, steel in the frames of the box coolers / ICAF system and vessels hull, stainless steel in the box cooler flanges.
• In particular, the integrated version of the ICAF system has shown itself not to be especially robust (loose wires, failing copper anodes, wrong current)
• The copper rods MUST be isolated from the vessel’s hull
• If they are not isolated from the hull, this can cause rapid corrosion (creating electrolytic currents between copper rods and the hull where the copper rods become cathodes and vessel’s hull becomes an anode)
• A working ICAF system does not prevent corrosion directly but indirectly, as reduced marine growth (barnacles) will reduce direct and indirect damage to the paint system (reduce the cleaning requirement while in dry dock)
RECOMMENDATIONS TO OWNERS
• Maintain box coolers and equipment according to manufacturer’s instructions, considering all aspects (box cooler maintenance, paint system of box coolers and vessel’s hull, ICAF system, sacrificial anodes); ensure that all makers are aware of the equipment of other manufacturers and the potential impact on the condition and function of “their” components, as well as the box cooler compartment in general
• Scope of work for maintenance of box coolers must be well defined / specified in the dry-docking specification submitted to shipyards (as most of the shipyards will quote for and conduct what is stipulated by owners)
• Discuss the quality and thickness of the coating system, material, size and installation of the anodes for the ICAF system and for the sacrificial anodes with the supplier(s) (or a reputable consultant), taking the vessel’s trading pattern and time till next dry-dock / inspection into account
• Ensure qualified supervision during dry-docking to control the work conducted regarding box coolers
• Share knowledge and understanding of the complexity of box coolers internally (superintendents and crew)
Guidelines to owners, surveyors and claims handlers when involved in box cooler cases
• Ensure early notification
• Joint survey when vessel is dry in dock
• Appreciate the potential complexity of the damage in way of box coolers / sea chests
• Ensure that involved persons have sufficient knowledge and understanding of this complex issue
• Provide and share all relevant information to specialists / surveyors / underwriters to help everyone understand the perhaps complex causation picture.
• Historic reports of previous maintenance work / dry-docking (what work was conducted how and by whom) can be important; details regarding historic trading areas, use of the vessel etc. can be valuable in understanding the cause and development of damage
• Be aware of the possible consequences of corrosion relating to the box cooler compartment and the potential impact of contributing factors: it is imperative that owners act quickly and diligently when early warning signs appear
• Learn by experience – owners should share knowledge with officers and crew on other vessels and amongst their onshore staff. In keeping with its knowledge sharing approach, Norwegian Hull Club will exchange appropriate information with surveyors, claims handlers, owners and other stakeholders.
NOTES:
1 Not properly cleaned / painted (i.e. not done according to manufacturer’s guidelines) or incorrectly cleaned and not painted (by shipyard), but reasonably also with a lack of information from owners on how it should have been done
2 Not observed in cases where Norwegian Hull Club has been claims lead but mentioned in other cases.
Norwegian Hull Club wishes you all fair winds and following seas.
• Questions? Please feel free to contact technical@norclub.com
REFERENCES
• Norwegian Hull Club Casualty Information Newsletter 99: Box Cooler Cleaning
• DNVGL tech and regulatory newsletter 2016
https://cathwell.com/safety-risk-due-to-severe-corrosion-related-to-box-cooler-arrangements/