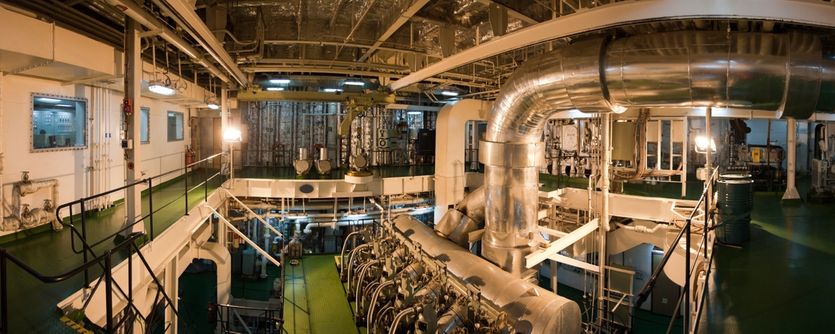
Sealing systems in watertight cable penetrations
Norwegian Hull Club wishes to emphasize increased safety on board with a focus on welfare, environment, assets and the distribution of useful experience
In this article we focus on the importance of correct sealing systems in watertight cable penetrations to avoid accidents.
Objective
Investigation of a number of engine room (E/R) flooding cases have revealed that wrongly installed E/R boundary cable penetration sealing arrangements contribute to the development and seriousness of accidents. The objective of this memo, which is developed by Cefor, is therefore to emphasise the risks associated with type approved cable penetrations when seal packing systems are not installed as per makers instructions nor subsequently sufficiently verified by the many parties involved; i.e. Flag States, Classification Societies, Owners and Shipyards.
Introduction
A general requirement in international rules concerning design of ships and offshore installations is that penetrations shall not inadmissibly impair the strength, tightness and fire resistance of the vessel’s hull structure. Type approved sealing systems are often used for this purpose, as they carry evidence of being designed and tested to ensure fireproof, watertight and/or gastight penetrations by cables and pipes in bulkheads and deck transits. Some systems are also tested and verified for resistance to shock and vibration as part of the type approval. It is therefore of greatest importance that each individual penetration sealing system installed is fit for its intended purpose as it acts as an important safety barrier contributing to the overall safety of the vessel.
For vessels, functional requirements to penetrations are set forth in SOLAS; fire integrity requirements are part of Reg.II-2/9.3, while watertight integrity requirements are found in Reg.II-1/13 and 13-1 for passenger- and cargo vessels respectively. Detailed design and test requirements for penetrations are specified in relevant international standards such as the Fire Test Procedures (FTP) Code as well as in rules set out by Classification Societies. This also means that the suitability of each penetration and sealing system is subject to approval and inspection by Flag States and/or Classification Societies as part of a vessel’s safety certificates. During a design phase, whether it being a vessel or offshore structure, the use of seal packings is determined in compliance with related rules. This process also applies for upgrading, modification etc. throughout the lifetime of the vessel/structure. During installation, the seal packing’s should be subject to verification by the Yard, Classification Society and Owner’s representative.
A seal packing system can consist of; a steel frame, wedge block(s) with bolts, modular blocks for filling out surplus space, and stay plates of steel or plastic.
Case Experience
The seal packing systems are regarded as relatively inexpensive and simple by design. Unfortunately, as the first case will demonstrate, the very installation of the seal packing system as a passive safety barrier has not been prioritized.
Insurance case 1: Container Vessel - GT 170,794 - Built: Denmark, 2005 - Class: ABS
In 2013, a large container vessel were in the southbound transit of the Suez Canal, Port Said. The vessel had passed point of no return when water ingress was observed in the shaft tunnel. Regardless of closing the watertight door and ventilation ducts, the main engine room was flooded when the seal packing systems in the bulkhead collapsed and the bilge system and ballast ejectors were unable to compensate for the water ingress. Investigation conducted by the Danish Maritime Investigation Board revealed amongst others;
“The cable penetration system was approved as a system and not as a single component on conditions that finally rested on the individual craftsman assembling the system” (….) “The craftsman did not have detailed knowledge about the status of the bulkhead as a whole” (…) “The classification survey process was not performed by a person with detailed knowledge of the cable penetration system. Therefore, the survey process rested on the type approval certificate ”.
The incorrect installation that led to the collapsed seal packing system has resulted in inspection of other vessels with Owners fleet to secure proper installation and thereby the water integrity.
Insurance Case 2: Drilling Rig - Built: China, 2012 - Class: DNV
During a yard stay in Norway, a rig built in China 2012 experienced an unfortunate damage and flooded a part of one pontoon to approx. 8 meters height. Some of the cable penetrations did not withstand the water pressure and “popped out”. Others were leaking, extending the flooded area of one pontoon and the damage to expensive equipment.
Subsequently, two different companies controlled the watertight cable and pipe penetrations in both pontoons. Many and different faults (with reference to makers set of criteria for correct installation) were observed, including a complete lack of MCT (multi cable transit) on two locations.
Insurance Case 3: General Cargo Vessel - GT 2.973 - Re-Built: Romania, 2002 - Class: BV
In January 2010, the vessel was on voyage in fully loaded condition from Klaipeda to Spanish ports. In a freezing cold Baltic sea, it was discovered that water ingress was filling up the vessel’s engine room aft, and the vessel was in danger of sinking. The first investigations indicated that the leakage could have originated in or in connection with the steering gear room aft. However, later investigations established that the water ingress originated from the emergency fire pump under the fo’c’sle, wherefrom it had penetrated the first water tight bulkhead and filled up the tunnel, before it penetrated the second watertight bulkhead entering into the engine room. It was also revealed that the cable openings in the mentioned bulkheads probably had not been equipped with any water tightening sealing at all when the vessel was rebuilt in 2002.
Summary and recommendations
With the cases presented, it appears that the integrity of seal packing systems is a challenge across vessel types, Yards, Classification Societies and Owners. It would not be possible to conclude only on a single cause to these costly incidents, as many parties are involved over a vessel’s lifetime. However, we do believe that a type approval certificate alone is not enough to ensure safety, as one of the contributing factors seems to be lack of ‘knowledge’ and ‘attention’ amongst the many parties involved in installation and verification of these seal packing systems. Therefore, we believe the following preventive measures should be taken:
• Inform Owners site team about the risks associated with type approved cable penetrations and emphasise the need for team members to possess the necessary competence to verify if seal packing systems are installed according to makers requirements.
• Include check of seal packing systems in the vessel’s Planned Maintenance System and dry docking program.
• Enhance tests and verification processes performed by Classification Societies for both newbuildings and annual surveys.