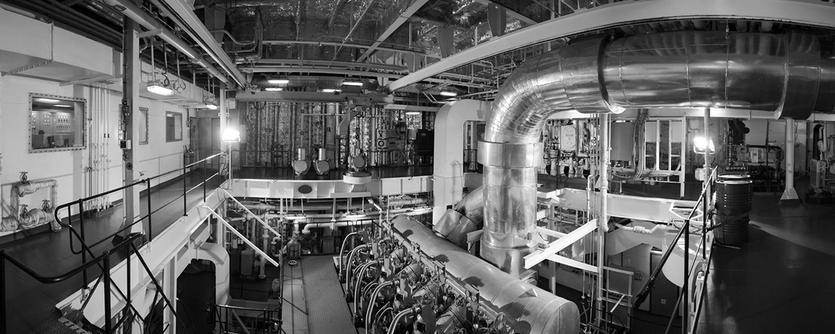
Engine Room fires
Norwegian Hull Club wishes to emphasise increased safety onboard with a focus on welfare, the environment, assets and the distribution of useful experience. In this newsletter, we focus on taking measures to help prevent fires in the engine room.
Dear Seafarer,
Norwegian Hull Club wishes to draw attention to the fact that it has registered 44 engine-room fires over the past ten years that were caused by leakages from Low Pressure Fuel and Lubricating Oil Pipes. These leaks resulted in oil igniting after coming into contact with hot surfaces.
Compared to fuel leakage from High Pressure Fuel Pipes, leakage from Low Pressure Pipes can be more serious due to the steady, voluminous flow of oil providing a continuous source of fuel to the fire until it runs out / is stopped.
Although many measures have been taken by the IMO, classification societies, owners, ship managers and engine manufacturers to prevent fires in engine rooms, Norwegian Hull Club still sees major fires of this type on board all types of vessels.
Causes identified by Norwegian Hull Club:
(1) Pipe connection failure. Damaged/worn pipe coupling. Incorrect torque applied.
(2) Loose studs on inlet/outlet flange to High Pressure Fuel Pump. Loose HP Pump foundation bolts.
(3) Pipe vibration. Insufficient pipe support. Fatigue.
(4) Crack in pipe welding /flange welding/pipe connections.
(5) Modification of pipe systems carried out –poor quality of work.
(6) Flexible hoses and hose connections worn/damaged.
(7) Overflow.
It is The Club’s belief that the frequency of such incidents can be reduced if proper preventative measures are taken.
Suggested preventative actions:
1. During newbuilding stage, fuel pipe installation (including insulation and cladding) is given more focus. Is Yard Standard Specification good enough? (Pipe routing, pipe supports-clamps, insulation and cladding quality/type). It is The Club’s experience that, once installed, any improvement is seldom considered.Check for pipe vibration (pipe tension and chafing – pipe clamp and support arrangement).Class survey of fuel and lube oil piping arrangement during newbuilding stage. Joint inspection prior delivery of the vessel.Assessment of the piping system including shielding of hot-spots.
2. During overhaul and repairs in service and in connection with scheduled/unscheduled yard stay:
Ensure that fuel and lubricating oil pipes that have been removed/replaced are reinstalled properly.Check fuel-pipe bends and connections for wear and cracks. Replace as found required.Ensure correct assembly of pipe flanges and fittings. Use correct torque. Check that pipe supports and clamps are in place.Pressure-test pipe system after re-installation. Insulation and cladding to be put back in place correctly. Work preferably to be included in the yard specification of repairs. Damaged insulation and cladding must not be reused.
3. Control of piping, insulation and cladding to be included in Planned Maintenance System:Assessment of engine room to identify risk areas (fuel/lube oil pipes with flanges/fittings that could in case of leakage spray onto hot surfaces). Tagging of risk areas for implementation into vessel`s Maintenance System.Pipe routing and connection condition inspection.After work is carried out on a system, pressure testing to be performed prior to refitting the insulation.Infrared temperature measurements (Hot spots - SOLAS 220°c).
Norwegian Hull Club wishes you all fair winds and following seas.