
Damage to controllable pitch propeller systems
In this Casualty Information newsletter, we would like to draw attention to an increase in occurrences of damage to controllable pitch propellers and associated systems.
Dear Shipowner, Manager and Seafarer,
In recent years, Norwegian Hull Club has noticed an increase in costly and time-consuming repairs to propulsion and thruster systems.
In most cases, repairs to propulsion propeller plants require docking and the ordering of major spare parts with long lead time. The number of days out of service, therefore, becomes significant.
We have handled several cases recently involving propulsion system failures that were reported a relatively short time after the vessels - or even a series of vessels - were delivered from the newbuilding yard, or after a main overhaul in connection with scheduled dockings or conversions.
Norwegian Hull Club is concerned about this increased number of occurrences and wishes to draw the attention of Owners, Technical Managers and Newbuilding teams to such damage and its possible causes.
Our findings are related to the following examples we have encountered:
1. Abrasive wear to movable components and parts due to debris and particles in the oil;
2. Incorrect piping quality used – not according to Class requirement;
3. Insufficient lubrication and filtration (wrong type of filters);
4. Insufficient flushing of the oil system prior to delivery;
5. Environmentally Acceptable Lubricants (EAL);
6. Sealing ring materials not suitable for the oil used;
7. Increased Total Acid Number (TAN);
8. Shaft earthing insufficient or incorrectly installed;
9. Incorrect component material standard used in the system.
10. Poor bonding of blade seals (vulcanization).
11. Twisting of blade seals causing leakages.
12. Incorrect procedures used when installing the propeller blade seals; yard has not followed the maker’s instructions.
For Controllable Pitch Propellers (CPP), the hydraulic oil system is a vital part of the propulsion plant. As for other hydraulic systems on board the ships, the CPP hydraulic system must be maintained to ensure it is clean and without any impurities that can damage internal seals and movable parts. It only takes a small number of particles in the oil system to increase the likelihood of damage and malfunction of components such as hydraulic control valves and sealing rings, which could lead to delayed manoeuvring response time.
Impurities that pass through filters can cause damage to internal components in the oil distribution system or propeller hub. Initially, this delays the propeller pitch response time and, after a while, can cause more serious damage and the resulting sudden loss of a vessel’s manoeuvring capability.
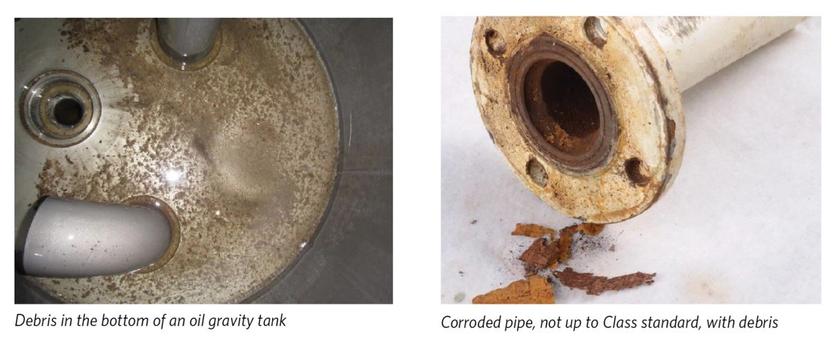
Prior to vessel delivery from a newbuilding yard or after a overhaul/conversion, the hydraulic oil system should be cleaned and properly flushed in accordance with the standard recommended by the CPP maker.
The hydraulic piping arrangement for propeller systems on board ships varies, as the hydraulic power pack/hydraulic pump station can be installed close to the propeller shaft or on the deck above. Consequently, the total length of piping systems also varies from installation to installation.
Pipe sections connected to the CPP (HP pipes) are normally supplied by the maker as part of the delivery. However, pipes running to / from header tanks and drains from the hydraulic power pack (HPU), for example, are usually delivered by the building yard.
It is crucial that the quality of these pipes and their connections delivered by the yard are class approved for use in hydraulic systems.
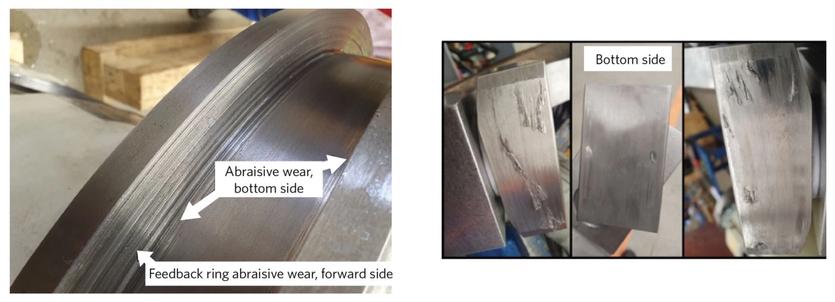
In addition, where hydraulic pipes are to be connected with welded sleeve couplings, class-approved standards must be followed. Even tiny pieces of welding slag and / or spatters that pass through a filter can potentially cause severe damage to a propeller plant’s internal seals and movable parts.
The quality of a system’s filter must be in accordance with the maker’s recommendation. Representative oil samples are to be drawn and laboratory analysis should be conducted in order to ensure oil-quality parameters are maintained within specification at all times, and to be able to take early action in accordance with the recommendations given by the laboratory.

RECOMMENDATIONS
Based on Norwegian Hull Club’s experiences with damage to propeller plants shortly after vessel delivery, we would recommend:
1. That filters, header tanks and power-pack tanks are regularly checked for impurities.
2. That representative oil samples are sent to a laboratory for analysis shortly after a vessel has been put into service following delivery. This to help identify any degradation in oil quality, as well as possible wear from the propeller system internal components at an early stage.
3. The building or repair yard, in cooperation with the system maker, prepares procedures that follow industry standards related to the flushing of the oil systems, prior to delivery. Proper testing of the system before and in connection with a sea trial should be carried out.
4. Propeller system maker’s procedures, recommendations and guidelines to be followed.
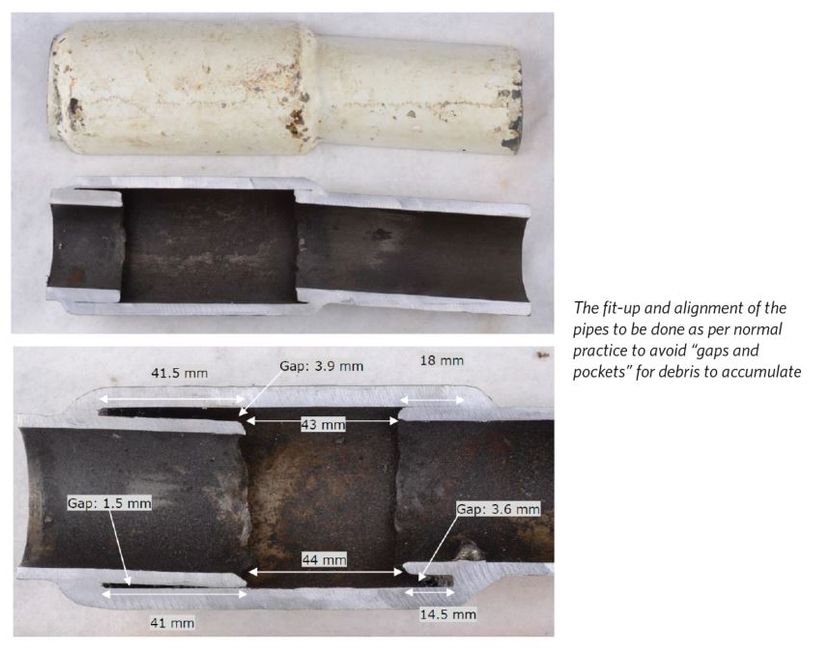
Norwegian Hull Club wishes you all fair winds and following seas.