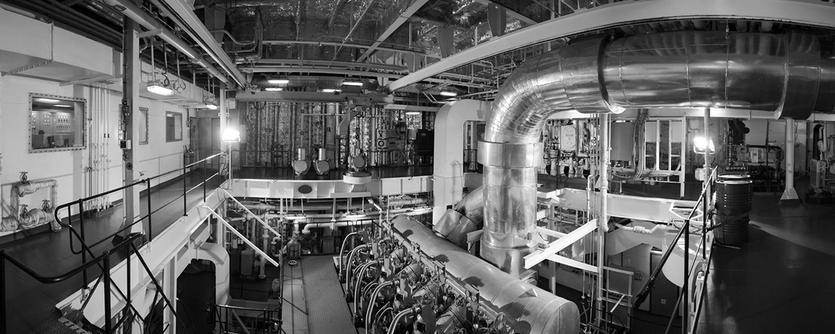
Damage involving 4-stroke engine main components
In this Casualty Information newsletter, No. 105, we look at damage to 4-stroke engine main components due to improper maintenance routines and procedures.
The Club receives frequent notification regarding damage to an engine’s main components, such as the crankshaft, rotation gear, vibration dampers, engine block and bedplate. We often find that such damage is due to improper maintenance procedures and failure during routine testing of the machinery.
In this Casualty Information Newsletter, we will focus on the increases we have observed relating to 4-stroke engine damage in recent years.
We see no direct link in this increase to maintenance being carried out by crews or by authorised companies. However, maintenance and routine tests should always be carried out in accordance with the engine maker’s instructions. Cause of damage has been shown on occasion to stem from the engine maker’s and associated equipment supplier’s maintenance and operation guidelines not being followed.
Damage to Engine Crankshaft, Cylinder Units and Engine Blocks
In recent years, damage to 4-stroke engines’ crankshafts and other main components have increased. Based upon the information we have collected during vessel surveys, we have looked into the possible causes of such serious damage that has, in some cases, resulted in the complete renewal of the engine and - even more seriously - injured crew members.
The question is, why we see increasing number of incidents with damage to engines, and what actions need to be initiated to reduce the number of cases?
We have recorded cases of sudden damage to crankpin bearings; this has resulted in the overheating of the crankpin followed by the piston becoming stuck fast in the cylinder liner and breaking the connection rod. The pistons and connecting rods have then been thrown out through the engine block and been found lying on the floor beside the engine.
In addition to damage to the engine, in the most serious cases, lubricating oil has leaked out from the damaged engine block and spread onto hot surfaces, resulting in fires and consequently severe damage to equipment in the engine room.
Based on our review of cases we have experienced at Norwegian Hull Club, below you will find recommended actions that we advise are taken in order to avoid serious or even catastrophic engine damage:
Cause No.1 – Impurities in the Lubricating Oil
• Frequent sampling of the lubricating oil to ensure proper oil quality at all time. The analysis reports should preferably be reviewed by the onboard Engineers and the vessel’s Superintendent (Technical Dept).
• Review the analysis reports and take actions in accordance with the analysis report’s comments and advices.
• Oil purifying quality to be verified (correct purifying temperature, flowrate and flushing intervals).
• Check condition of filters and ensure that the filter inserts are of correct type and mesh (micron).
• Check the condition of the filter housing and ensure that the filter inserts are installed correctly, plus that the seal rings/packings are in place. Relevant for both Manual and Auto Filters.
• For all filters, check condition of the over-pressure valve (by-pass valve) and that the valve is opening at correct set-point.
• For non-disposable filter inserts/candles, check the general condition and that the filters are properly cleaned. Ultrasonic cleaning or other methods. Note: The filter-mesh will deteriorate over time, hence the inserts should be replaced when damaged or when found impossible to clean. Check estimated filter inserts lifetime from instruction manual.
• In connection with main overhaul, the engine sump tank to be cleaned properly. Lubricating oil coolers, pumps, valves and pipelines to be flushed through prior filling new oil.
Cause No.2 – Maintenance/incorrect mounting procedures
• Regarding routine overhaul, ensure that the connection rod bolts are tightened to the correct torque.
• Note that the connecting rod bolts normally have a maximum lifetime, hence bolts have to be replaced according to the engine maker’s guidelines.
• Check that tools are in good condition (torque spanners and hydraulic jacks and pumps).
• Measure the connection rod bearing housing ovality and check the general condition.
• Tolerances and measuring method in accordance to Engine Maker’s instruction manual.
• Check the general condition of crank pins and surface roughness. If possible, measure the crankpin (measurement method and condition checks as per engine maker’s instructions).
Cause No.3 – Shaft Alignment
• Crankshaft deflection measurements. Take regular measurements and fill in data in the engine maker’s deflection form. Evaluate results as per instructions in the engine operation manual. If in doubt, consult the engine maker in order to confirm that the measurements results are within the recommended tolerances.
• If the engine foundation (engine-generator skid) is installed on flexible pads/chocks, condition and measurement checks need to be performed according to the engine maker’s instructions. Note that there might be a maximum lifetime of the flexible pads, as the quality will deteriorate over time.
• Check engine vibration. Control of vibration damper according to engine maker’s instruction manual. Note: In case of fluid-filled vibration dampers (i.e. silicon filled), regular analysis of the liquid to be performed according to instruction manual.
• Any observation of increased engine vibration, the cause of the vibration to be verified before continue operating the engine.
Cause No.4 – Over-speed Tests
• The engine over-speed shut down is required to be tested regularly and in accordance with the engine maker’s instructions.
• Some engines are equipped with a mechanical overspeed device, some with electrical over-speed protection, and some with both types of over-speed systems included in the engine Safety System.
• Due to incidents with uncontrolled testing of the overspeed devices, we would recommend that the crew conducts a Risk Assessment prior to the test.
• One of the barriers to avoid that the engine reach rpm above the recommended level during the overspeed test is to have a crew member stand-by to stop the engine/close the fuel inlet to the engine in case the engine does not stop at the preset revolution. (Overspeed rpm setpoint).
Cause No.5 – Engine Maker’s Service Bulletins
• In order to keep their customers updated on new developments within Design, Services and Operation Guidelines and International Rules & Regulations, engine makers are regularly releasing service bulletins as a method of reaching out with the information to shipowners and managers, and not least to the crews onboard the ships.
• During repair surveys, we observe that not all owners and managers have procedures in place to ensure that these service bulletins are distributed and made known on board.
• Relevant information from such service bulletins relating to maintenance should be taken into consideration in connection with major repairs to be entered into the vessel’s maintenance system.
Recommendations
By sharing our experiences from surveys related to damage on board clients’ vessels, Norwegian Hull Club aims to highlight possible measures that can be taken to prevent serious incidents occurring.
We therefore recommend that close attention is paid to following engine and equipment makers’ maintenance and operation instuctions. It should also be ensured that such instructions are the latest versions available.
It is crucial that all relevant instructions and guidelines are well known to all personnel involved in the operation and maintenance of engines on board.